صفر تا صد تولید سیم و کابل
مقدمه: شریانهای حیاتی دنیای مدرن
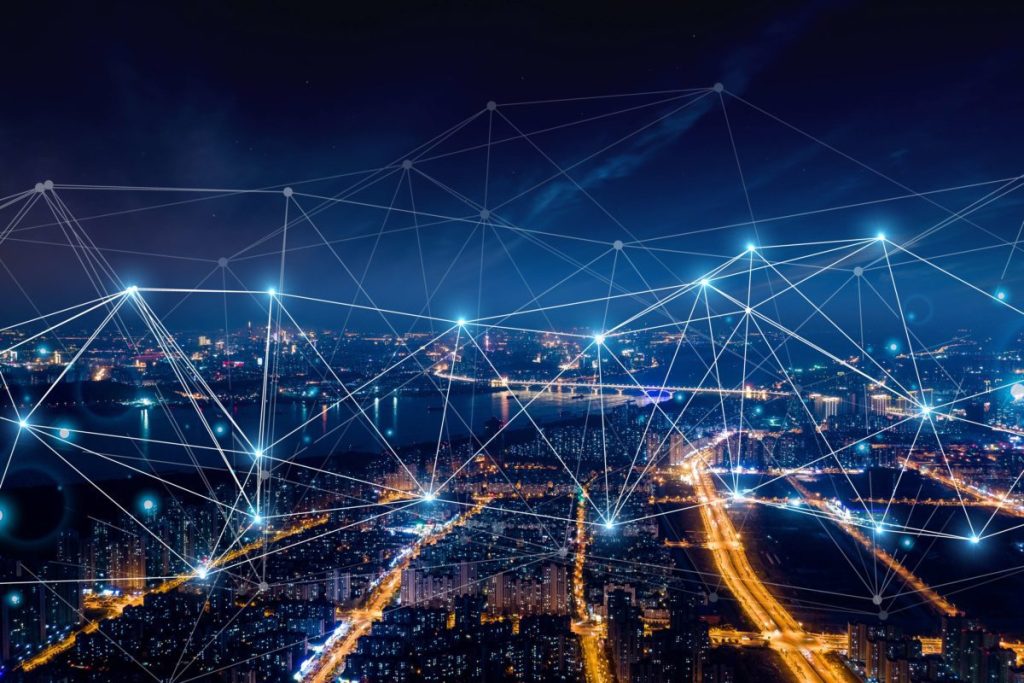
در دنیای امروز، تصور زندگی بدون برق و ارتباطات غیرممکن است. از روشن کردن یک لامپ ساده گرفته تا انتقال دادههای پیچیده در شبکههای جهانی، همه و همه به وجود شریانهای حیاتی به نام سیم و کابل وابسته هستند. اما این اجزای بهظاهر ساده، چگونه از مواد اولیه خام به محصولاتی با این درجه از اهمیت و دقت تبدیل میشوند؟
این محتوای تخصصی و آموزشی، شما را به سفری شگفتانگیز در خط تولید سیم و کابل میبرد. از لحظه ورود مواد اولیه تا بستهبندی نهایی محصول، گامبهگام با فرآیندهای پیچیده و دقیق این صنعت آشنا خواهید شد. هدف ما ارائه دیدی جامع و عمیق، مناسب برای متخصصان، دانشجویان، علاقهمندان و هر کسی است که میخواهد بداند پشت این محصولات ضروری چه دانش فنی و دقتی نهفته است. با ما همراه باشید تا رازهای تولید سیم و کابلهای باکیفیت را کشف کنیم.
بخش ۱: مواد اولیه – بنیان کیفیت
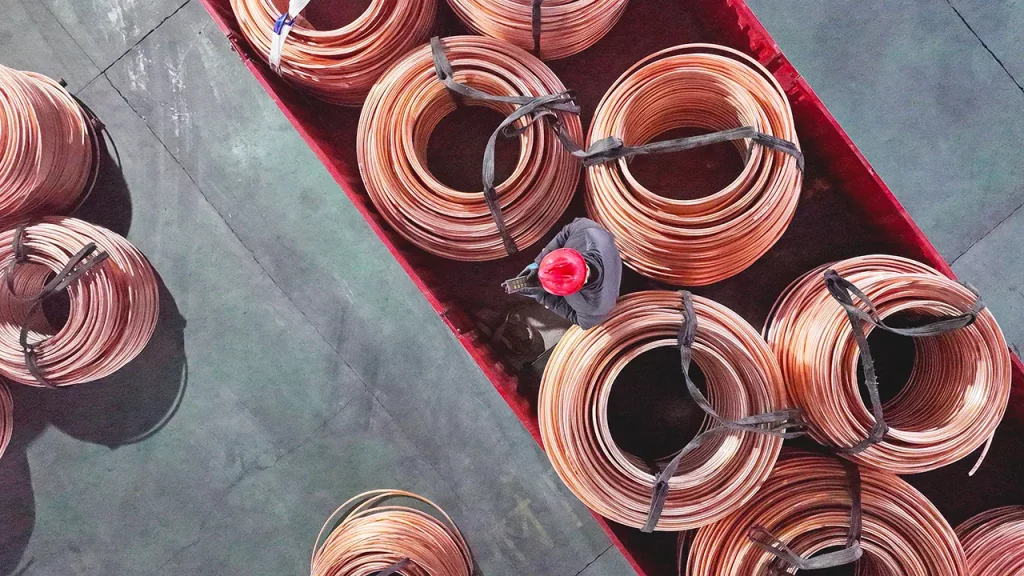
هر سازه مستحکمی، بر پایههای قوی بنا میشود. در صنعت سیم و کابل نیز، کیفیت محصول نهایی ارتباط مستقیمی با کیفیت مواد اولیه دارد. دو دسته اصلی مواد اولیه در این صنعت عبارتند از:
1. هادیها (Conductors): فلزات رسانا
مس (Copper): پرکاربردترین هادی به دلیل رسانایی الکتریکی فوقالعاده بالا، انعطافپذیری خوب و مقاومت در برابر خوردگی. مس معمولاً به صورت مفتول مسی ۸ میلیمتری (Copper Rod) وارد کارخانه میشود که خلوص آن (معمولاً ۹۹.۹٪ به بالا) نقشی حیاتی در کیفیت نهایی دارد.
آلومینیوم (Aluminum): سبکتر و ارزانتر از مس است، اما رسانایی کمتری دارد (حدود ۶۰٪ مس). به دلیل وزن کمتر، در خطوط انتقال هوایی و کابلهای قدرت بزرگ کاربرد فراوانی دارد. آلومینیوم نیز معمولاً به صورت مفتول آلومینیومی (Aluminum Rod) با قطر مشخص (مثلاً ۹.۵ میلیمتر) تهیه میشود.
2. عایقها و روکشها (Insulation & Sheathing): پلیمرهای محافظ
پلیوینیل کلراید (PVC – Polyvinyl Chloride): رایجترین ماده عایقی و روکشی به دلیل قیمت مناسب، انعطافپذیری خوب، مقاومت در برابر شعله (ذاتاً خودخاموششونده است) و مقاومت شیمیایی قابل قبول. PVC در گریدها و ترکیبات مختلف برای کاربردهای گوناگون (مانند مقاوم در برابر روغن، دمای بالا یا پایین) تولید میشود. این ماده به صورت گرانولهای PVC وارد کارخانه میشود.
پلیاتیلن (PE – Polyethylene): دارای خواص الکتریکی عالی (ثابت دیالکتریک پایین)، مقاومت بسیار خوب در برابر رطوبت و انعطافپذیری بالا بهویژه در دماهای پایین است. انواع مختلفی دارد:
LDPE (پلیاتیلن با چگالی پایین): انعطافپذیرتر.
HDPE (پلیاتیلن با چگالی بالا): سختتر و مقاومتر در برابر سایش.
XLPE یا XPE (پلیاتیلن شبکهای شده – Cross-linked Polyethylene): این نوع PE با فرآیندی شیمیایی یا فیزیکی “کراس لینک” میشود که مقاومت حرارتی آن را به شدت افزایش میدهد (تا ۹۰ درجه سانتیگراد و حتی بالاتر). XLPE بهترین عایق برای کابلهای قدرت فشار متوسط و قوی است. PE و XLPE نیز به صورت گرانول تهیه میشوند.
لاستیکها و الاستومرها (Rubbers & Elastomers): مانند EPR (اتیلن پروپیلن رابر) و سیلیکون رابر، برای کاربردهایی که نیاز به انعطافپذیری بسیار بالا، مقاومت در برابر دمای خیلی بالا یا پایین، یا مقاومت در برابر مواد شیمیایی خاص دارند، استفاده میشوند.
مواد کمدود بدون هالوژن (LSZH/LS0H – Low Smoke Zero Halogen): این ترکیبات پلیمری ویژه، در هنگام سوختن دود بسیار کمی تولید کرده و گازهای سمی و خورنده هالوژنی (مانند کلر) آزاد نمیکنند. استفاده از آنها در مکانهای عمومی و حساس (مترو، تونل، بیمارستان، مراکز داده) برای افزایش ایمنی در زمان آتشسوزی ضروری است.
بخش ۲: کشش مفتول (Wire Drawing) – ظرافت در شکلدهی
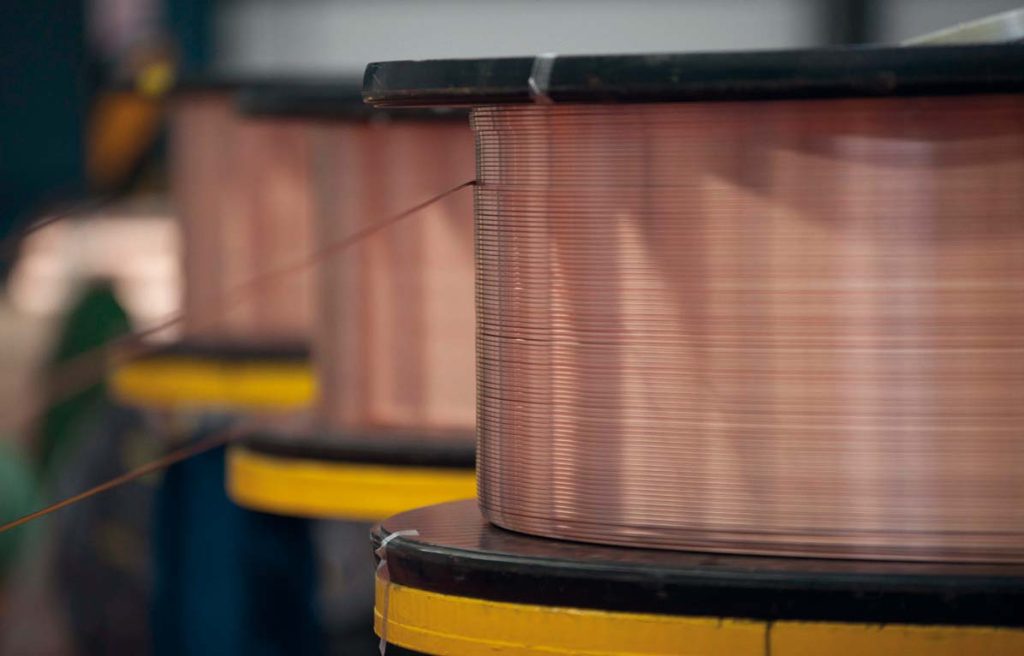
مفتولهای ضخیم مس یا آلومینیوم (Rod) برای تبدیل شدن به سیمهای نازک مورد استفاده در کابلها، باید فرآیند کشش (Drawing) را طی کنند.
فرآیند: مفتول اولیه از میان مجموعهای از قالبهای کشش (Drawing Dies) عبور داده میشود. هر قالب، قطری کمتر از قالب قبلی دارد. این قالبها معمولاً از مواد بسیار سخت مانند الماس صنعتی (PCD – Polycrystalline Diamond) یا تنگستن کارباید ساخته میشوند تا در برابر سایش مقاوم باشند.
کشش چندمرحلهای (Multi-stage Drawing): برای رسیدن به قطرهای بسیار نازک (حتی تا چند صدم میلیمتر)، مفتول از تعداد زیادی قالب پشت سر هم عبور میکند. سرعت کشش در هر مرحله افزایش مییابد تا حجم فلز عبوری ثابت بماند.
روانکاری و خنککاری: در طول فرآیند کشش، به دلیل اصطکاک و تغییر شکل پلاستیک، حرارت زیادی تولید میشود. استفاده مداوم از مایعات روانکننده و خنککننده ضروری است تا از آسیب به مفتول و قالبها جلوگیری شده و کیفیت سطح سیم حفظ شود.
آنیلینگ (Annealing) / بازپخت: فرآیند کشش باعث سخت شدن فلز (Work Hardening) و کاهش انعطافپذیری آن میشود. برای بازگرداندن نرمی و انعطافپذیری لازم به سیم (بهویژه در مس)، از فرآیند آنیلینگ استفاده میشود. در این فرآیند، سیم در یک کوره با اتمسفر کنترل شده (معمولاً نیتروژن یا بخار آب برای جلوگیری از اکسیداسیون) تا دمای مشخصی گرم شده و سپس به آرامی سرد میشود. آنیلینگ میتواند به صورت جداگانه پس از کشش یا به صورت پیوسته (Inline Annealing) در همان ماشین کشش انجام شود.
بخش ۳: تاباندن رشتهها (Stranding/Bunching) – انعطاف و قدرت
بهجز در موارد خاص (سیمهای مفتولی یا تکرشتهای)، هادیها معمولاً از تابیدن تعدادی سیم نازک (رشته) به دور هم ساخته میشوند. این کار چندین مزیت مهم دارد:
افزایش انعطافپذیری: یک هادی رشتهای بسیار انعطافپذیرتر از یک هادی تکمفتولی با سطح مقطع مشابه است.
افزایش مقاومت در برابر خستگی: رشتهها در برابر خم و راست شدن مکرر مقاومت بیشتری دارند.
سهولت نصب: انعطافپذیری بیشتر، نصب کابل را آسانتر میکند.
انواع اصلی تاباندن:
تاباندن منظم (Concentric Stranding): رشتهها به صورت لایههای منظم و هممرکز به دور یک رشته مرکزی تابیده میشوند. جهت تابش هر لایه معمولاً مخالف جهت لایه قبلی است تا ساختار پایدار بماند. این نوع تاب برای هادیهای گرد و فشرده (Compacted) مناسب است.
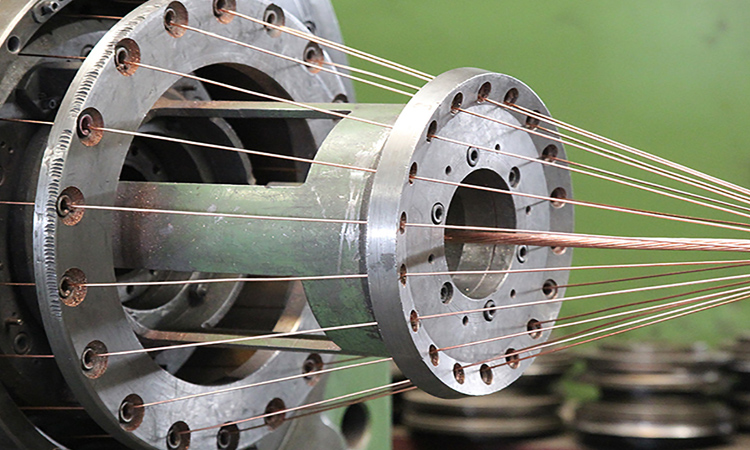
بانچینگ یا تاباندن نامنظم (Bunching): تمام رشتهها بدون نظم خاصی و در یک جهت به هم تابیده میشوند. این روش سادهتر است و انعطافپذیری خوبی ایجاد میکند، اما ساختار هادی به اندازه تاب منظم، پایدار و گرد نیست.
طنابی یا کمپکت (Rope Lay / Compact Stranding): برای هادیهای با سطح مقطع بسیار بزرگ، ابتدا چند دسته رشته به صورت منظم یا نامنظم تابیده شده (استرند فرعی) و سپس این استرندهای فرعی مانند طناب به دور هم تابیده میشوند. در نوع کمپکت، پس از تاباندن، هادی از قالب فشردهسازی عبور میکند تا فضای خالی بین رشتهها کاهش یافته و قطر نهایی کمتر شود.
ماشینهای استرندر (Stranding Machines) با چرخش قرقرههای حاوی رشتههای نازک به دور محور مرکزی، این فرآیند را انجام میدهند.
بخش ۴: عایقکاری (Insulation) – جداسازی و حفاظت الکتریکی
مهمترین وظیفه عایق، جداسازی الکتریکی هادی از محیط اطراف و سایر هادیها است. این کار توسط فرآیندی به نام اکستروژن (Extrusion) انجام میشود.
دستگاه اکسترودر (Extruder): قلب خط تولید عایقکاری است. اجزای اصلی آن عبارتند از:
قیف تغذیه (Hopper): گرانولهای پلیمر (مانند PVC یا XLPE) در اینجا ریخته میشوند.
سیلندر (Barrel): یک لوله فلزی که توسط هیترهای الکتریکی گرم میشود.
مارپیچ یا ماردون (Screw): یک مارپیچ گردان درون سیلندر که مواد را به جلو رانده، فشرده کرده و حرارت اصطکاکی ایجاد میکند تا پلیمر ذوب شود.
کلهگی و قالب (Crosshead & Die): در انتهای اکسترودر، مذاب پلیمری ۹۰ درجه تغییر مسیر داده و از طریق یک قالب دقیق (Die) به دور هادی که از مرکز آن عبور میکند، کشیده میشود. نوک قالب (Tip یا Mandrel) قطر داخلی عایق (روی هادی) و قالب بیرونی (Die) قطر نهایی سیم عایقشده را تعیین میکند.
فرآیند: هادی (که ممکن است قبل از ورود به کلهگی پیشگرم شود) با سرعت ثابت از مرکز کلهگی عبور میکند. همزمان، اکسترودر مذاب پلیمری را با فشار و دمای کنترلشده به درون کلهگی تزریق میکند. مذاب دور هادی را فرا گرفته و شکل قالب را به خود میگیرد.
خنککاری: بلافاصله پس از خروج از قالب، سیم عایقشده وارد یک کانال طولانی آب سرد (Cooling Trough) میشود تا پلیمر به سرعت جامد شده و شکل خود را حفظ کند.
کنترل کیفیت حین فرآیند: ضخامت و هممرکز بودن (Concentricity) عایق بسیار مهم است. سیستمهای اندازهگیری لیزری یا اولتراسونیک به طور مداوم این پارامترها را کنترل میکنند. همچنین تست جرقهزن (Spark Tester) ولتاژ بالایی را به سیم اعمال میکند تا هرگونه سوراخ یا نقص ریز در عایق را شناسایی کند.
بخش ۵: کابلسازی (Cabling/Assembly) – تجمیع هستهها
در کابلهای چندرشته (Multi-core Cables)، سیمهای عایقشده (که حالا “هسته” یا Core نامیده میشوند) باید به شکل منظمی به هم تابیده شوند تا ساختار کابل نهایی شکل بگیرد.
فرآیند تابیدن هستهها: مشابه فرآیند استرندینگ هادیها، هستههای عایقشده از روی قرقرههای مجزا باز شده و با نظم مشخصی (معمولاً به صورت لایهای) به دور هم تابیده میشوند.
فیلرها (Fillers): برای پر کردن فضاهای خالی بین هستههای تابیده شده و ایجاد یک مقطع گرد و یکنواخت برای کابل، از مواد پرکننده (فیلر) مانند رشتههای پلاستیکی (معمولاً پلیپروپیلن PP) یا پودر استفاده میشود. این کار به پایداری ساختار کابل کمک میکند.
نوار پیچ (Taping): گاهی اوقات، یک یا چند لایه نوار (معمولاً پلیاستر یا نوار میکا برای مقاومت در برابر آتش) به دور مجموعهی تابیده شده پیچیده میشود تا هستهها را کنار هم نگه دارد و یا خواص خاصی (مانند مقاومت در برابر آتش) به کابل بدهد.
کابلهای زوجی (Paired Cables): در کابلهای مخابراتی و شبکه، دو سیم عایقشده ابتدا به صورت زوج به هم تابیده میشوند (Pair Twisting) تا اثرات نویز الکترومغناطیسی (Crosstalk) کاهش یابد. سپس این زوجها با هم تابیده میشوند.
ماشینهای کابلسازی (Cabling Machines) این عملیات را انجام میدهند که میتوانند بسیار بزرگ و پیچیده باشند، بهویژه برای کابلهایی با تعداد رشتههای زیاد.
بخش ۶: روکشزنی (Sheathing/Jacketing) – لایه نهایی محافظ
پس از اینکه هستههای کابل به هم تابیده و آماده شدند، یک لایه محافظ نهایی به نام روکش (Sheath یا Jacket) روی آنها اعمال میشود. این لایه وظایف مهمی دارد:
حفاظت مکانیکی: محافظت از هستههای داخلی در برابر سایش، ضربه، فشار و کشش در هنگام نصب و بهرهبرداری.
حفاظت شیمیایی: مقاومت در برابر روغنها، مواد شیمیایی، حلالها و عوامل محیطی.
مقاومت در برابر عوامل جوی: مقاومت در برابر رطوبت، اشعه ماوراء بنفش خورشید (UV) و تغییرات دما.
مقاومت در برابر آتش (در صورت نیاز): جلوگیری از گسترش شعله یا تولید دود و گازهای سمی (در کابلهای LSZH).
فرآیند روکشزنی نیز مشابه عایقکاری، توسط اکستروژن انجام میشود. مجموعه هستههای تابیده شده (با یا بدون فیلر و نوار) از مرکز کلهگی اکسترودر عبور کرده و مذاب پلیمری (معمولاً PVC، PE، LSZH یا لاستیک) به عنوان روکش روی آن اعمال میشود. سپس کابل روکششده خنککاری میشود.
زره (Armoring): برای کابلهایی که نیاز به حفاظت مکانیکی بسیار بالا دارند (مانند کابلهای دفنی مستقیم در زمین یا محیطهای صنعتی خشن)، یک لایه زره فلزی بین عایق داخلی (Bedding) و روکش نهایی (Outer Sheath) قرار میگیرد. زره میتواند به صورت نوار فولادی گالوانیزه (Steel Tape Armor – STA) یا سیمهای فولادی گالوانیزه (Steel Wire Armor – SWA) باشد. لایه Bedding (معمولاً PVC یا PE اکسترود شده) زیر زره قرار میگیرد تا از آسیب دیدن هستهها توسط زره جلوگیری کند.
بخش ۷: تست و کنترل کیفیت (Testing & Quality Control) – تضمین عملکرد و ایمنی
کیفیت و ایمنی، حرف اول را در صنعت سیم و کابل میزند. هر مرحله از تولید تحت نظارت و کنترل دقیق قرار دارد، اما پس از تکمیل ساخت کابل، مجموعهای از آزمونهای نهایی (Final Tests) طبق استانداردهای ملی (مانند ISIRI در ایران) و بینالمللی (مانند IEC, VDE, BS, UL) روی محصول انجام میشود تا از انطباق کامل آن با مشخصات فنی اطمینان حاصل گردد. مهمترین تستها عبارتند از:
تستهای الکتریکی:
مقاومت هادی (Conductor Resistance): اندازهگیری مقاومت الکتریکی هادی در واحد طول برای اطمینان از رسانایی مناسب و سطح مقطع صحیح.
تست ولتاژ بالا (High Voltage Test): اعمال ولتاژ بسیار بالاتر از ولتاژ نامی کابل بین هادیها و بین هادی و زمین (یا شیلد/زره) برای اطمینان از عدم وجود ضعف یا سوراخ در عایق.
مقاومت عایقی (Insulation Resistance): اندازهگیری مقاومت الکتریکی لایه عایق برای اطمینان از کیفیت آن.
تستهای ظرفیت خازنی و اندوکتانس (Capacitance & Inductance): برای کابلهای مخابراتی و داده.
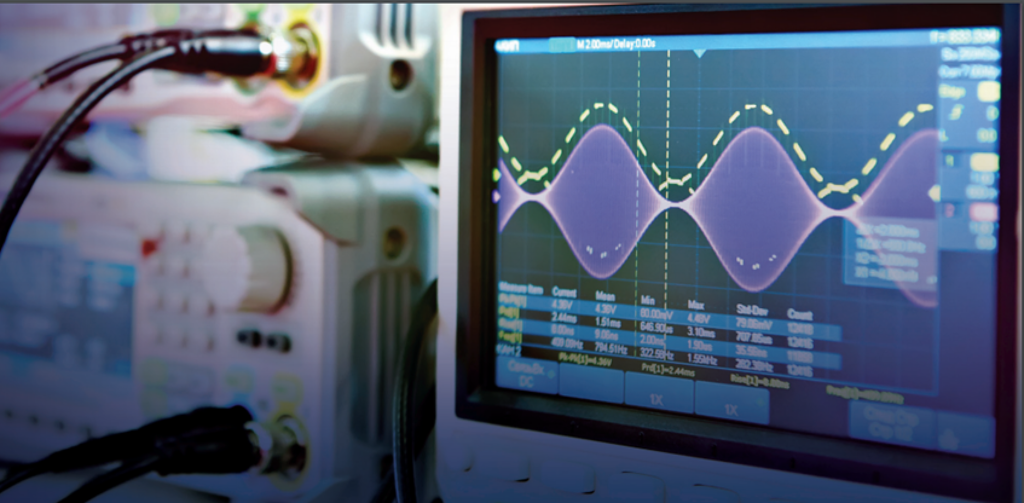
تستهای مکانیکی و فیزیکی:
اندازهگیری ابعاد (Dimensional Checks): کنترل دقیق قطر هادی، ضخامت عایق و روکش، قطر نهایی کابل با استفاده از تجهیزات اندازهگیری دقیق (مانند میکرومتر، کولیس، پروفایل پروژکتور).
تست کشش و ازدیاد طول (Tensile Strength & Elongation): اندازهگیری استحکام کششی و میزان افزایش طول عایق و روکش قبل از پارگی برای ارزیابی خواص مکانیکی پلیمرها.
تستهای مقاومت در برابر حرارت (Heat Shock, Cold Bend, etc.): بررسی رفتار عایق و روکش در دماهای بالا و پایین.
تستهای خاص:
تست شعله (Flame Retardancy Test): بررسی میزان مقاومت کابل در برابر گسترش آتش طبق استانداردهای مختلف (مانند IEC 60332).
تست دود و گازهای اسیدی (Smoke Density & Halogen Acid Gas Test): برای کابلهای LSZH.
تست مقاومت در برابر روغن، UV و …
تنها کابلهایی که تمامی این تستها را با موفقیت پشت سر بگذارند، تأیید شده و آماده عرضه به بازار میشوند.
(ویژگیهای سئو: کلمات کلیدی “کنترل کیفیت سیم و کابل”، “تست کابل”، “استاندارد سیم و کابل”، “تست ولتاژ بالا”، “مقاومت عایقی”، “تست شعله IEC 60332”)
بخش ۸: مارکینگ و بستهبندی (Marking & Packaging) – شناسایی و حملونقل
مارکینگ (Marking/Printing): اطلاعات ضروری مانند نام سازنده، نوع کابل، سایز هادی، ولتاژ نامی، استاندارد تولید، و گاهی متراژ به صورت پیوسته روی روکش نهایی کابل چاپ میشود. این کار معمولاً با استفاده از پرینترهای جوهرافشان یا لیزری در انتهای خط تولید انجام میشود. مارکینگ واضح و بادوام برای شناسایی و ردیابی کابل ضروری است.
بستهبندی (Packaging): کابل نهایی بر اساس طول و وزن، روی قرقرههای چوبی (Wooden Drums)، قرقرههای فلزی (Steel Drums)، قرقرههای پلاستیکی (Plastic Spools) یا به صورت کلاف (Coils) پیچیده میشود. بستهبندی مناسب، از آسیب دیدن کابل در حین حملونقل و انبارداری جلوگیری میکند. اطلاعات کامل محصول روی برچسبی به قرقره یا کلاف الصاق میشود.
نتیجهگیری: دقت، تخصص و تعهد به کیفیت
همانطور که مشاهده کردید، تولید سیم و کابل فرآیندی چند مرحلهای، پیچیده و نیازمند دانش فنی بالا، تجهیزات پیشرفته و کنترل کیفیت دقیق در هر گام است. از انتخاب هوشمندانه مواد اولیه تا آزمونهای سختگیرانه نهایی، هدف اصلی، تولید محصولی ایمن، قابل اعتماد و با عملکرد بهینه است که بتواند نیازهای متنوع دنیای مدرن را در انتقال انرژی و اطلاعات برآورده سازد.
درک عمیق این فرآیندها نه تنها به ما کمک میکند تا به اهمیت این محصولات پی ببریم، بلکه در انتخاب و استفاده صحیح از انواع سیم و کابل نیز راهگشا خواهد بود. صنعتی که با دقت و تخصص، شریانهای حیاتی تمدن ما را تولید میکند، شایسته توجه و تقدیر است.